Business Inventory | Part 1 – The Essentials For Understanding Inventory
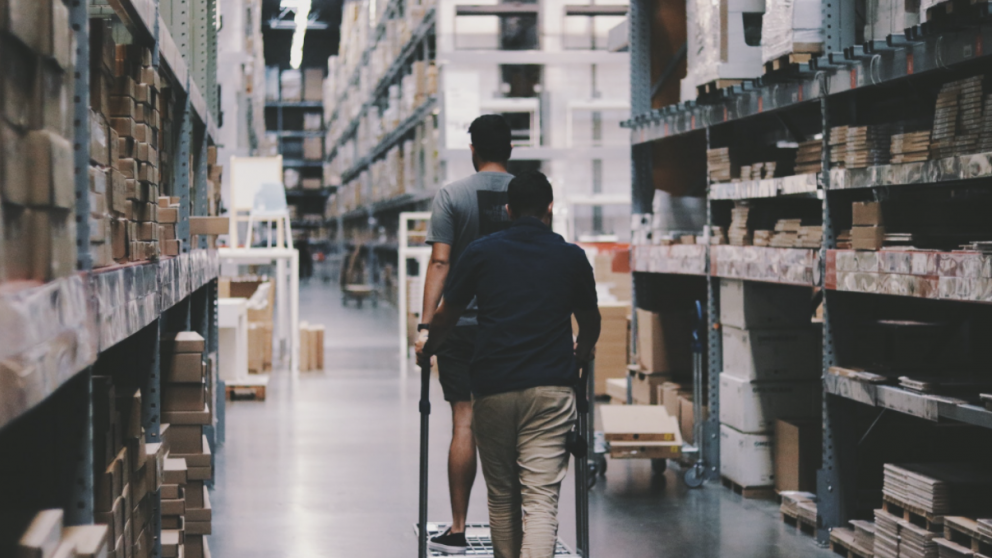
Inventory is a cost for some and security for others. It makes an accountant nervous and makes a foreman giddy. But when does a business have too much inventory? And how does a business reduce that inventory without getting rid of valuable products?
Business inventory is defined as:
“Inventory, in business, is any item of property held in stock by a firm, including finished goods ready for sale, goods in the process of production, raw materials, and goods that will be consumed in the process of producing goods to be sold. Inventories appear on a company’s balance sheet as an asset.” – Britannica
As we see in the definition, there are some broad categories applied to the concept. In essence, there are three, basic forms of inventory:
- Raw Materials
- In Production Goods
- Finished Goods
To understand how a business can reduce inventory, management for that business must first establish the forms of inventory it handles. Once this has been categorized, then the process for inventory reduction can efficiently begin.
In this article from Auction Masters, we’ll walk readers through the 3 basic types of inventory most businesses encounter. We’ll then give our readers 3 profit-making actions for reducing the inventory in their businesses. Believe it or not, there is a ton of value to be found in reducing inventory, from monetary gains to streamlining production processes.
Remember, the objective of inventory management is keeping enough product on the shelves and in circulation to meet customer demand while not creating a glut of unusable, unsellable overstock.
The function of inventory is to meet customer demand. As consumer markets and commercial environments pivot with more frequency, controlling the flow of inventory has become an essential part of any business model that offers a product. It is now imperative to place inventory cost in the top section of any company’s operation list to manage and track.
In the past, traditional business models allowed companies to maintain a steady level of inventory because the competition was usually low and the products’ design and function were not being updated very often. Now, companies in virtually any industry encounter a list of competitors, fluctuating markets, and quickly evolving products and features that can quickly result in unused inventory hitting the bottom line of businesses pretty hard in the ‘losses’ category.
So what do the benefits of mitigating and reducing inventory look like? Let’s first gain a better understanding of the 3 types of inventory as they relate to a business.
As we mentioned above, inventory can be broken down into 3 basic categories:
- Raw Materials
- In Production Goods
- Finished Goods
1) Raw Materials
Quite often, company warehouses don’t just hold finished products. There are plenty of manufacturers that use distribution centers to store raw materials for their production lines.
Warehouse workers monitor raw materials to make sure the operations continue. If raw materials run too low or too high, problems can arise. And the concept of raw materials doesn’t only refer to ‘manufacturing assets’. We must consider all of the assets that factor into processing and distributing raw materials.
Here’s an example: A company is forced to stop its supply chain because the factory ran out of shipping containers. It’s imperative for factory managers to track any business tool critical for processing raw materials through operations. There are many great inventory control software and barcoding solutions available to help workers label containers, vehicles, and any other assets to keep them under constant supervision. Once a team can quantify the materials they have in the warehouse, they can track and replenish those materials at the right time and in the correct amount.
2) In Production Goods
As inventory moves down the distribution line, it goes from raw material to ‘in production’ goods. During this step of the process, goods often return to the warehouse before they are ready to sell. If not properly labeled and categorized, employees may confuse ‘in production’ goods stored on shelves for finished goods that are ready for sale and distribution. Employees need to use some sort of automated data collection system to update the status on each piece of inventory.
This has often proved to be a make or break step in streamlining the production cycle for goods and materials. There is nothing more frustrating for a warehouse foreman or production manager than having materials reach the production floor only to be lost, incorrectly categorized, or stored in the wrong place.
In this instance, a uniform solution across the company can be most helpful. When a business provides all of its’ different departments with uniform tools, it greatly prevents communication and processing errors. This will allow for better production results with less inventory.
3) Finished Goods
This is a pretty straightforward concept in the line of distribution. Finished goods have made it to the end of the production cycle and are ready for selling to customers. Finished goods are also sometimes classified as ‘cycle products’ because they are shipped to the business and sold to the consumer very quickly with little-to-no time spent on the shelf.
When products arrive from a supplier or complete the manufacturing process, it is vital to have steps in place that help the company keep those products organized and ready for processing. Employees will greatly benefit from having orderly, streamlined procedures for keeping track of these finished goods and their movements through the supply chain.
This allows for a smooth transition into the distribution of goods with the slightest amount of error. Once again, organization of inventory and understanding the amount of material in the warehouse help tremendously in getting the produced goods processed and distributed.
If you’ve read our articles throughout this year, you’ll know that research shows successful businesses putting their customer’s needs at the forefront. One of the most critical contributors to giving a customer the best experience possible is ensuring their products arrive on time.
Understanding the types of inventory your business may handle is an important prerequisite for creating profits with inventory management and reduction. Once you
In Part 1, we’ve explored the 3 basic types of inventory most businesses encounter.
If you have any questions about reducing inventory in your warehouse or business, give the team at Auction Masters a call today. We’ve helped thousands of businesses reduce inventory and liquidate their business equipment over the last 4 decades. Let our experts help you make the most informed decisions about your business equipment.
In the meantime, explore Part 2 of this series where we’ll give readers 3 profit-making actions for reducing inventory in their businesses.